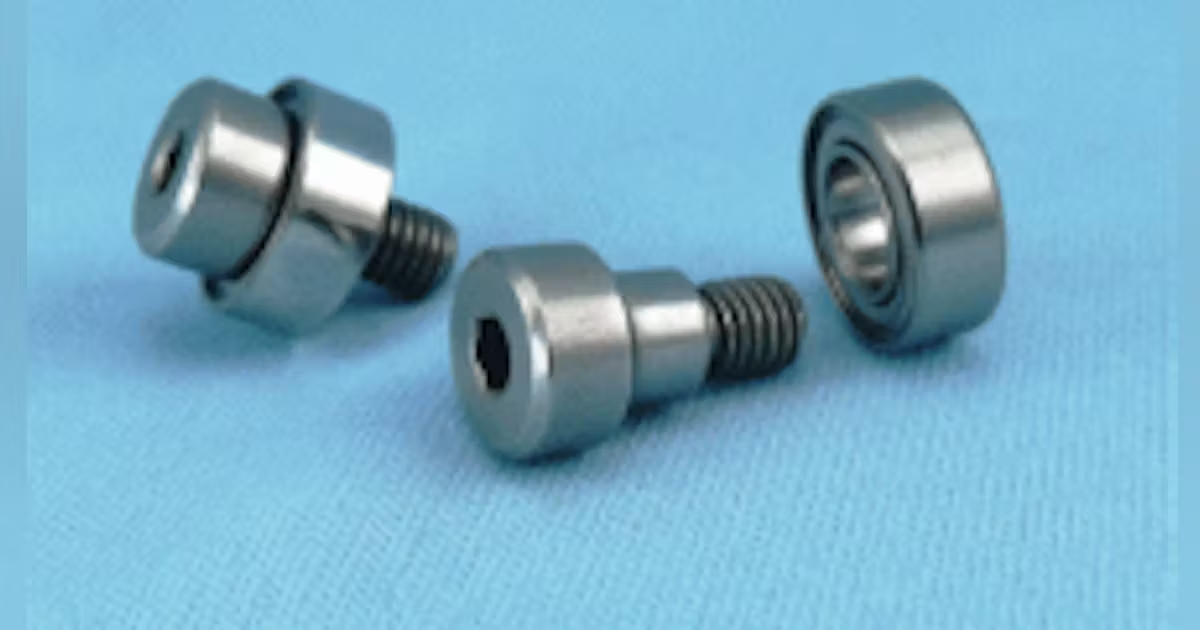
How to Find the Perfect Fasteners for Your Equipment
When it comes to assembling and maintaining machinery or other equipment, finding the right fasteners is crucial. Using the appropriate fasteners ensures the longevity, safety, and efficiency of the equipment. This guide will help you navigate through key considerations and steps in choosing the perfect fasteners, such as shoulder screws and conventional metal stamping, for your equipment.
Looking for Quality Shoulder Screws: Ensure Precision and Durability
One of the most important types of fasteners for certain equipment is the shoulder screw. Shoulder screws, also known as shoulder bolts, are precision-engineered fasteners that feature a cylindrical shoulder between the head and the threaded portion. This shoulder allows for rotation and axial movement, making them ideal for applications that require bearings or rotating parts.
When searching for the perfect shoulder screws, the first priority should be quality. These screws must be made from durable materials such as stainless steel, alloy steel, or brass, depending on the application’s environmental demands. Stainless steel shoulder screws, for example, offer resistance to corrosion, making them suitable for use in outdoor equipment or machinery exposed to harsh conditions.
Additionally, the shoulder screw’s dimensions—such as the diameter of the shoulder, the length of the thread, and the overall size—should be considered based on the specific equipment requirements. Always ensure that the shoulder screw fits precisely in the design to prevent any issues with wear and tear or misalignment. Consult manufacturers who can provide custom specifications or specialized options for complex equipment designs.
Avail Conventional Metal Stamping: Ensure Versatility and Cost Efficiency
Another important consideration when selecting fasteners is the manufacturing process. Conventional Metal Stamping is a widely used method for producing metal parts, including fasteners. It involves shaping and cutting metal sheets through a process of stamping presses that use dies to create intricate designs. For fasteners, this process ensures uniformity and precision, making it an ideal option for producing large quantities of components like washers, clips, and brackets.
When sourcing fasteners through Conventional Metal Stamping, the main advantage lies in both the versatility and cost-effectiveness of the process. Stamping allows for the rapid production of high-volume parts at a relatively low cost, which can be beneficial for businesses requiring large quantities of fasteners.
Furthermore, metal stamping can accommodate various metal types, such as steel, aluminum, and brass, providing a diverse range of material options based on your equipment’s needs. Whether you’re looking for lightweight, corrosion-resistant materials or heavy-duty options, the conventional metal stamping process can produce fasteners that meet your exact specifications.
It’s also important to consider the design capabilities of metal stamping. The process allows for the production of fasteners with intricate designs, ensuring a perfect fit for complex assemblies. You can often request additional features such as slots, holes, or raised areas to improve the functionality of your fasteners.
Additional Tips for Choosing Fasteners for Your Equipment
Beyond specific fastener types like shoulder screws and manufacturing techniques like conventional metal stamping, there are several other factors to keep in mind when selecting fasteners for your equipment:
- Strength and Load Capacity: Make sure the fastener you choose can handle the specific load requirements of your equipment. For high-stress applications, opt for fasteners made from high-strength alloys or heat-treated materials.
- Corrosion Resistance: For equipment exposed to harsh environments or chemicals, it’s important to choose fasteners that are resistant to rust and corrosion. Stainless steel, zinc-plated, and coated fasteners are great choices for these conditions.
- Thread Type: The threading on the fastener should be compatible with the material you’re fastening. Consider whether you need coarse or fine threads, and ensure that the threading matches the threading of the holes or nuts it will be used with.
- Size and Fit: Measure the required size carefully to ensure the fasteners fit perfectly. Ill-fitting fasteners can cause stress on the equipment and lead to failure.
- Safety: Consider any safety implications of the fasteners you choose. Ensure that they will not easily come loose due to vibration or other external forces. You may want to use locknuts, thread adhesives, or safety washers for additional security.
Conclusion
Finding the perfect fasteners for your equipment requires careful consideration of various factors, such as material, durability, size, and manufacturing methods. Shoulder screws, with their unique design and function, are excellent for applications requiring rotation or axial movement, while conventional metal stamping offers cost-effective and precise production of fasteners. By carefully evaluating the specific needs of your equipment and sourcing high-quality fasteners, you can ensure the efficiency, longevity, and safety of your machines.